成功の本質
第98回 duAro(デュアロ)/川崎重工業
完全自動化を目指さず発想の転換が生んだ人共存型ロボット
川崎重工業西神戸工場のショールームに置かれているデュアロ。ほかのロボットの周囲には安全柵があるのに、ここにはない。
Photo=笹木淳
人とロボットが同じ生産ラインで"肩"を並べて共同作業を行う。これにより、従来、ロボットを使えなかった工場でも自動化を進めることができる。「人共存型」の双腕ロボットとして、2015年6月の発売以来、年間販売台数1000台とヒットを飛ばしているのが、川崎重工業の「duAro(デュアロ)」だ。産業用ロボットではこれまで、よく売れる製品でも年間数百台が上限だった。
デュアロは上部のアーム部分と下部の箱形の台車部分からなる。最大の特徴は、台車の真ん中に立つ軸に取りつけられた左右2本のアームによって、人が両腕で行う作業を再現できることだ。それぞれのアームは人の上腕、前腕、手に相当する3つのパートで構成される。各パートは互いに軸で連結され、これが関節となって、左右どちらにも水平方向に回転する。加えて、手の部分は上下方向にも動かすことができる。このように複数の関節を持ち、水平方向にアームが回転する水平多関節ロボットで双腕型はデュアロが世界初だ。
開発の拠点がある川崎重工業西神戸工場(兵庫県神戸市)のショールームで、デュアロのデモンストレーションを見学した。実物は高さ約170センチ、幅53センチ、奥行き約72センチ。人1人分のスペースに設置できる。
最初は、スマートフォン(スマホ)の保護フィルム貼りだ。画面を拭く→保護フィルムを持ちシートを剥がす→気泡が入らないように画面に貼り、表面を押さえて密着させる。一連の動作を左右のアームが協調しながらこなす。2017年にソフトバンクとタイアップし、携帯電話ショップで人型ロボット「ペッパー」が案内役を務めて実験的に行ったサービスの再現だ。その横では、ピザの生地にソースを塗り、オーブンに入れて焼く動作や、握った寿司飯にワサビを塗り、ネタをのせる動作を披露し、外食産業にも導入が可能であることをアピールする。
突きつけられた"挑戦状"
長谷川省吾 氏
川崎重工業
精密機械・ロボットカンパニー
ロボットビジネスセンター
FAソリューション第二総括部長
Photo=笹木淳
川崎重工業は1968年に日本で初めて産業用ロボット事業を開始して以来、小型から大型まで多様な分野に製品を送り出してきた。ロボット業界のパイオニア的存在がデュアロを開発することになったのは、ある企業経営者によって"ロボット屋の挑戦心"に火をつけられたのが始まりだった。
2014年春、同社のロボットビジネスセンター長の橋本康彦(現・取締役常務執行役員)は登壇したある講演会の懇親会で、1人の人物と同じテーブルで隣り合わせに座った。スマホなどの電子部品をEMS(電子機器製造受託サービス)で生産する会社の社長だった。
その会社は中国広東省南部の港湾都市、珠海に工場を持っていたが、社長は「残念ですが、うちの工場ではロボットは使えません」と語った。橋本は「わが社は幅広く製品を取りそろえているので、ぜひ使ってみてください」と勧めたが、社長は「いや、あなたはわかっていない」と言い張る。「それなら、一度、工場を見せてください」と橋本は食い下がった。
その年の夏、橋本は幹部社員を連れ、香港からフェリーで珠海に渡った。技術部門からはロボットビジネスセンターFA・クリーン総括部FAシステム部長の長谷川省吾(現・FAソリューション第二総括部長)が同行した。橋本も、長谷川もロボット開発一筋の筋金入りのロボット屋だ。一行は3つの工場を丸一日かけてじっくり見て回った。結果、社長の言い分が正しかったことを納得させられ、"敗北"を認めざるを得なかった。その後、開発プロジェクトのリーダーを務めた長谷川が話す。
「問題は、工場でつくる製品のライフサイクルの短さでした。スマホはモデルチェンジが早いため、部品を発売前3カ月間でつくり溜めします。それが生産のピークで、おおむね半年後には生産中止になり、次のモデルのための新しいラインが組まれます。一方、われわれがつくる産業用ロボットは、安全柵で囲むなど、導入前のさまざまな調整に3カ月は要します。1つのモデルの生産が3年から5年続く自動車工場などでは成り立っても、ピークが3カ月で、半年で生産が終わるラインの準備に3カ月もかけていたら、まったくペイしないのは当然でした」
「この工場にロボットを入れられますか」。社長から"挑戦状"を突きつけられたロボット屋は、ここに未開拓のニーズを発見し、その場で、「導入可能なロボットをつくってみせます」と約束し、商品開発を決意した。「では、2週間後に提案をお待ちしています」。産業用ロボット業界では考えられないほど短い期限は、スマホ業界ではいかにスピードが求められているかを物語った。
Photo=川崎重工業提供
価格は人件費以下に
一刻の猶予も許されない。一行は帰途につくフェリーのなかで開発のコンセプトを練り始めた。求められたのは、発想の転換と"割り切り"だった。
ラインをすべて自動化する従来のやり方では、ラインが頻繁に変わるスマホの部品工場には受け入れられない。全工程をカバーする発想はこの際、捨てる。そして、人が行ったほうが効率的な複雑な作業と、そうでない簡単な作業に分け、簡単な作業について人からロボットに置き換える。これならば先方にも使ってもらえそうだ。
人の代わりをするとすれば双腕が必要で、サイズも人と同じくらいにしなければならない。ラインの変更に合わせ、移設も自由にできるようにする。安全柵も設置に時間と費用がかかるので不要にする。コストの問題も重要だ。中国人従業員の平均年収は約100万円。24時間3交代制ならば年間300万円。価格はこれ以下に抑える。
もう1つの大きな課題は、2週間という短期間で案をつくらなければならないことだった。ゼロから新しいロボットを考える余裕はない。既存の技術をいかに組み合わせるか。珠海の工場では、多くの従業員がずらりと並んで作業していたが、ほとんどが机の上で両腕を水平方向に動かす作業だった。同じ動きをする製品が自社にあった。半導体製造工場で、集積回路のチップを切り出すシリコンウエハー(円盤状の板)を移動させる単腕の搬送ロボットだ。世界シェアは50%を超え、技術が確立されている。これを2本組み合わせて双腕にする。
こうして一行は、フェリーが香港に着くまで、わずか1時間で何枚ものスケッチを描き、製品の基本コンセプトを固めた。ここに、川崎重工業が50年に及ぶロボット開発の歴史のなかでも初めて挑戦する「人共存型」のコンセプトが生まれた。長谷川が話す。
「人共存型ロボットの概念は欧米で先行して提起されながら、なかなか具体的な導入には至っていませんでした。われわれも初めから人共存型ロボットをつくろうと考えたわけではありません。珠海の工場に入れることのできるロボットをつくろうとして、発想を転換し、割り切りをした結果、人共存型にたどり着いたのでした」
Photo=川崎重工業提供
安全性の担保で苦闘
人体に当たっても大丈夫なようにアームカバーはウレタン製になっている。
Photo=川崎重工業提供
人共存型ロボットを開発するため、組織体制も従来とはまったく異なる形がとられた。本来、新しいロボットの開発は開発部が担う。長谷川が部長を務めるFAシステム部は、顧客の状況に合わせ、自社のハードとソフトを組み合わせて提案する業務を担当していたが、このプロジェクトでは開発を主導することになったのだ。この変更は川崎重工業にとって、1つの転換を意味した。
「産業用ロボットの開発はこれまで、こんな機能、こんなスペックが必要だろうと、予想される顧客の要望の最大公約数に当てはまるようにつくるという発想で行われてきました。一方、このプロジェクトではライフサイクルの短い製品をつくるという限定された領域で、顧客の要望に的確に応えるには、どんなものが最適で、どう具現化するかという、まったく逆の発想が求められました。社内でも、これからはシステム部隊がお客さまの要望を把握し、それを起点にロボットをつくっていかなければならないという声が出ていました。デュアロはその第1号になったのです」(長谷川)
人共存型ロボットの開発には、想定外の困難がともなった。安全柵を設置しないため、並んで作業をする人とロボットとの"接触"にかかわる課題が次々と持ち上がったのだ。FAシステム部で設計を担当した村上潤一(現・クリーン設計部)が話す。
「大きな課題は、人に怪我をさせない安全性をいかに担保するかでした。当時、具体的な基準はどこにもありませんでした。アームが持てる重さの上限は2キロで十分と想定し(2018年発売のデュアロ2は3キロに増量)、低出力のモーターを採用する。万が一、人とロボットが衝突したら、衝突検知機能によりロボットを停止させる。衝突で人体にどれくらい力がかかったら停止させるかという度合いも、腕と腹部では変えるといった細かな対策を講じましたが、より難しかったのは、ロボットからいかに"硬さ"を取るかでした。アームに巻くクッションも人と接触する可能性の高い部位はより柔らかくする。見た目も重要で、どんな材質を使えば、当たっても痛くなさそうなサラサラ感を出せるのか、かなり気を使いました。従来のロボットづくりではまったく考えなかったことに神経を使わなければならなかったのです」
想定外の業界から受注
村上潤一 氏
川崎重工業
精密機械・ロボットカンパニー
ロボットビジネスセンター
FA・クリーン総括部
クリーン設計部
Photo=笹木淳
デュアロは、動作の手順をインプットする方法も簡略化した。「ダイレクト教示」といって、現場で作業者がアームをつかみ、手順に沿って動かしながら直接教えることができるので、専門的知識を必要としない。教示の面でも人共存を可能にした。
2014年の年末にはプロトタイプを作成。翌2015年6月に1台280万円で販売を開始し、珠海の工場に納品した。アームにつけるアタッチメントを変えることでさまざまな作業ができることをアピールすると、ほかのEMS企業や電気電子部品のメーカーなどからも受注が相次いだ。
そのなかには、まったく予想外の食品業界からの受注も入っていた。
コンビニの弁当を製造する工場では、朝と昼とでつくられる商品が変わるなど、スマホの部品工場以上に生産ラインの変動が激しいため自動化が難しく、人海戦術に頼ろうにも人手不足が深刻化していた。ファストフード産業からも、ハンバーガーのパテを焼く作業に導入できないかという引き合いがあった。さらに意外だったのは銀行からのアプローチだった。店舗でのデスクワークは平面作業が多いこと、ロボットならば個人情報の漏洩の心配がないことなどから、活用を検討したいとの申し入れがあった。長谷川が話す。
「産業用ロボット業界はこれまで、完全自動化工場の実現を目指してきました。その一方で、ロボットが入れない生産現場も次々出てきたのに、あまり目を向けてきませんでした。しかし、デュアロはそんな現場にもどんどん入っていける。複雑な作業は人が引き受ける形で人がちょっと手助けしてやれば、人共存型ロボットが活躍する場はもっともっと増えていくでしょう」
双腕の外観が人間の体をイメージさせるのか、導入している顧客企業のなかには、デュアロの上部に"顔"をつけ、ニックネームで呼んでいる例もあるという。
ものを動かす作業を行うさまざまな現場で、人とロボットが同じ空間を共有しながら、それぞれが得意な作業を分担し、トータルで効率化を図る。人手不足の解消策として、そんな"人・ロボット協業時代"の到来をデュアロは予期させる。(本文敬称略)
Text=勝見 明
現場で暗黙知を共有
知識創造が生み出した機動的イノベーション
一橋大学名誉教授
産業用ロボットの開発について、主体(つくり手)と客体(顧客)との関係性を見てみよう。川崎重工業では従来、主体と客体を明確に分け、客体を外から傍観者的に分析するアウトサイドインのアプローチがとられてきた。
「完全自動化」というつくり手の理想論を前提に、分析をもとに製品に求められる要件を演繹的に導き出す。そして、どのケースにも当てはまるよう、「最大公約数」を引き出して製品化する。しかし、珠海のスマホ部品工場の現実をアウトサイドインで分析的にとらえていたら、自動化は不可能と判断されたはずだ。
これに対し、長谷川氏らの一行はインサイドアウトのアプローチをとった。顧客と一体となる主客未分の境地で、工場の現実の文脈そのもののなかに入り込み、五感を駆使して感じとる。そして、「完全自動化」という理想論を前提とした演繹ではなく、製品に求められる要件を帰納的に導き出そうとした。
それも単なる帰納法ではなかった。「顧客は何でも自動化を求めているわけではない」という現場に埋め込まれた暗黙知を感じとると、「ロボットができる作業についてだけ、人に代わってロボットがラインに入る」と、発想をジャンプさせるアブダクション(仮説生成)により、人共存型ロボットのコンセプトを生み出すに至った。
このプロセスを知識創造理論の視点でなぞってみると次のようになる。現場で顧客と暗黙知を共有する、と同時にメンバー同士でも暗黙知を共有し(共同化)、そこから仮説を立て、コンセプトを導き出して、形式知に変換した(表出化)。
さらに、半導体製造工場で使うウエハー搬送ロボットの技術という、組織に蓄積された形式知を組み合わせるモデルを考え出し(連結化)、2週間という短期間での立案を可能にした。
このプロジェクトでは開発部ではなく、システム部が初めて開発を進めた。その過程では、顧客が感じる安全性とは何かといった本質的な議論を深めるなど、一人ひとりが人共存型ロボットについての新たな暗黙知を体得していったはずだ(内面化)。それは必ずや、次の開発に活かされることだろう。
デュアロは、まさにSECI(セキ)モデル(*)によるイノベーションの成功例にほかならない。知識創造プロセスをスパイラルに循環させ、人共存型ロボットを日本でさらに進化させていくことを期待したい。
(*)知識創造理論の中核となるモデル。個人の暗黙知からグループの暗黙知を創造する「共同化」、暗黙知から形式知を創造する「表出化」、個別の形式知から体系的な形式知を創造する「連結化」、形式知から暗黙知を創造する「内面化」の4つの知識変換モードを経る。
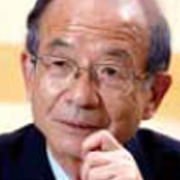
野中郁次郎氏
一橋大学名誉教授
Nonaka Ikujiro 1935年生まれ。早稲田大学政治経済学部卒業。カリフォルニア大学経営大学院博士課程修了。知識創造理論の提唱者でありナレッジマネジメントの世界的権威。2008年米経済紙による「最も影響力のあるビジネス思想家トップ20」にアジアから唯一選出された。『失敗の本質』『知識創造企業』など著書多数。